Over the past several days, I’ve continued work on the tail section. I completed drilling the longerons on each side and am now working on the top skins. The aft skin is completely drilled and ready for the forward skin next. It was more of the same with using a lot of clecos to align everything well and positioning the stiffeners correctly to drill new holes. The structure is much more rigid with the addition of the L-shaped longerons and top skin. This whole process just includes a lot of match drilling and final drilling. I’m already thinking about all of the deburring that needs to be done!
I again got to break out a tool that has never been used, the fluting pliers. Several of the flanges on the ribs need to be “heavily fluted,” whatever heavily means. I started by putting a good squeeze and it turned out to be right on. Beginner’s luck. Fluting the metal puts a kink in a flat piece so that the metal can bend around a curve and still have a 90 degree flap on it.
I also had a first (but probably not last) injury related to the project. While drilling a longeron, I had my index finger on the back side a little too close and managed to put a #40 drill into the finger tip. Fortunately my lightning fast reflexes (and the drill stop) prevented it from sinking in any further and I got away with just a band aid and sore finger.
Finally, I’ve been working on the preliminary electrical system design. It’s very early but I am a systems guy and also want to plan ahead. So I started with the switches that I wanted in the panel to ensure I have enough of the Aveo RockRack switches I want to use. Of course, I missed one cover kit with all the lights and now can’t find them anywhere. Very frustrating, as they are being discontinued and Aircraft Spruce no longer has the covers I need in stock. I’m following a couple of leads now to see if I can get my hands on them and will grab a couple extra switches if I can put the whole plan together. If not, it will be back to the drawing board.
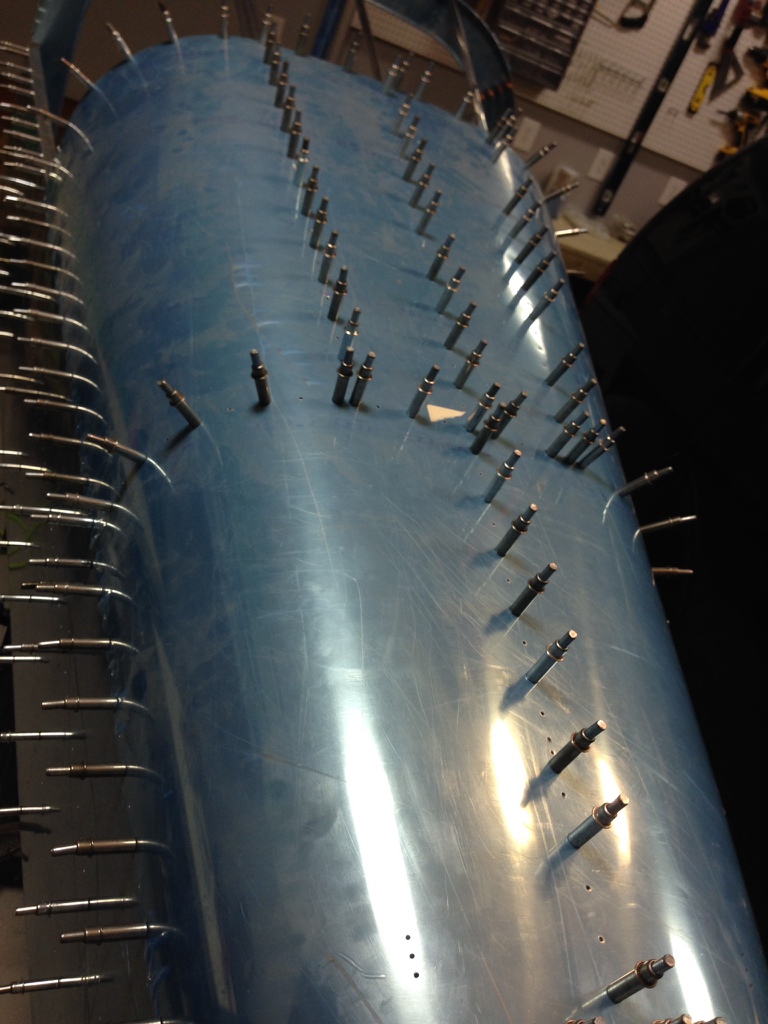
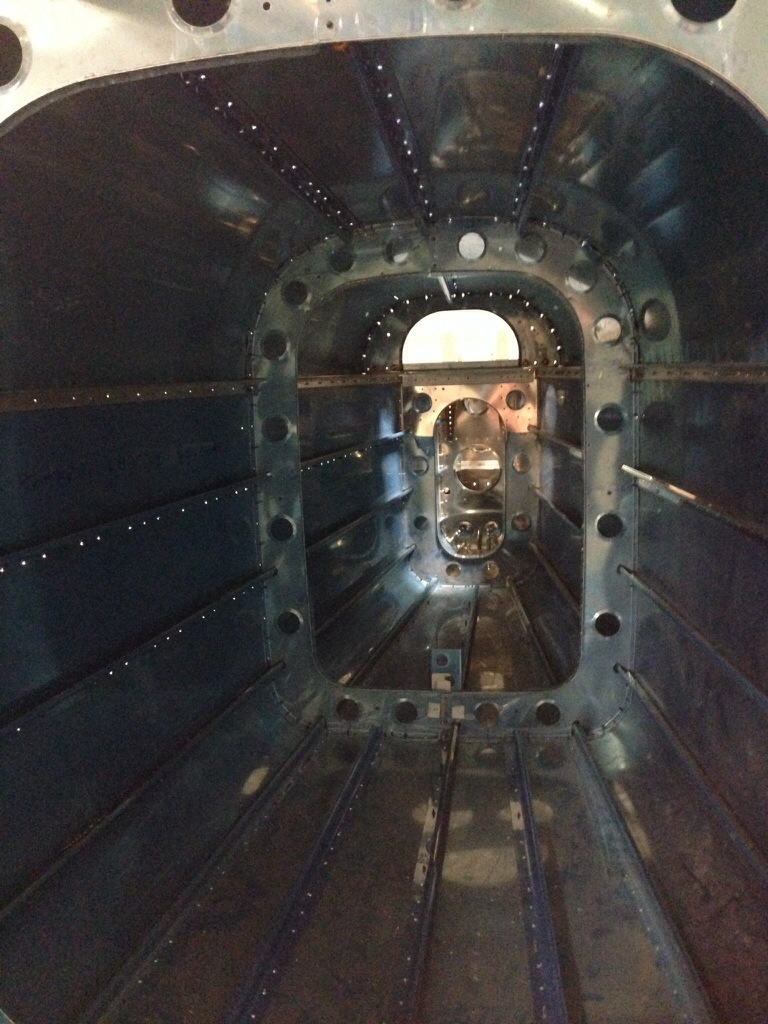